Vertical Lift Storage for Parts Departments: Adams Morey
Adams Morey, a premier DAF and commercial vehicle maintenance company in the Southwest, faced a significant challenge when relocating to their new Bridgwater site. To support their expanding operations, they needed to maximise the number of service bays for vehicle repairs while ensuring all other departments ran at tip-top performance – including their critical parts department. Adams Morey turned to Industore for a comprehensive design and solution to futureproof their new facility, maximise the number of service bays available, and provide true transformation.
The new stores demanded an innovative approach to space management. With a diverse inventory ranging from tiny bolts (just a few centimetres in size) to bulky air filters and whole van panels, Adams Moreyâs traditional shelving system at their former facility was overflowing, limiting storage capacity and creating inefficiencies. To make room for the required nine-bays within the new workshop, the parts department footprint had to be reduced – while improving functionality, efficiency, and storage capacity.
A Proven Partnership
Industore has worked with Adams Morey for nearly two decades, starting with the installation of two Hänel Lean-Lifts at their Devon facility in 2006. These machines remain operational today, under Industoreâs Comfort+ plan – a testament to their reliability and the quality of service plans Industore offers. This longstanding relationship gave Adams Morey the confidence to entrust Industore with the complex requirements of their Bridgwater facility.
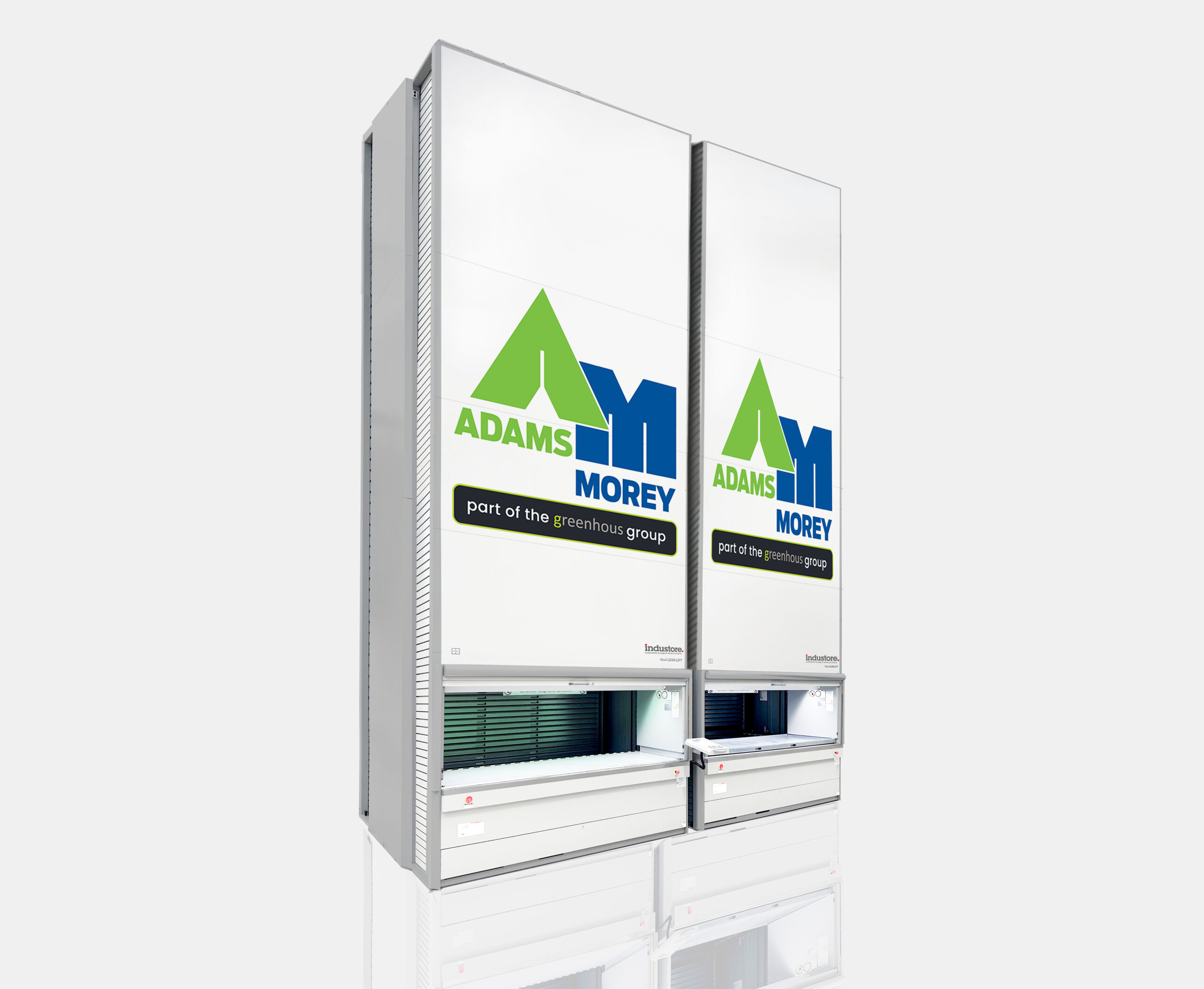
Mick Dean, Parts Manager at Adams Morey Bridgwater:
âWe knew Lean-Lifts were reliable, because our earliest two are still operating, some twenty-years later, but we wanted Industore because we were looking for more than vertical lift storage. We needed the whole facility designed to ensure we could really make it work with the nine-bay option. That means the parts department had to be âas big as needed, but as small as possibleâ – if that makes sense, and we really knew that only Industore who could do that for us.
Industore designed the entire storage department, from the vertical lift storage through to the mezzanine and racking – everything. Industoreâs sister company, Powell, also offers interior design and fit-outs, so they were even able to design the new offices, boardrooms, reception areas, kitchens, facilities, and more for us – even down to specifying and supplying the furniture to fit in these spaces. The whole process was handled on our behalf by Industore, cradle to grave, which is exactly what we needed for this project.â
Top Five Lean-Lift Features:
By using the full vertical height of the facility, the Lean-Lifts (vertical lift storage) halved the size of the planned stores, safeguarding the hopes of a nine-bay workshop.
The Lean-Liftsâ height detection system measures every tray on return to store, rendering the updated tray to the optimal location. This allows Adams Morey to seamlessly adjust their parts or stock levels to meet changing demand, while ensuring excellent storage that is organised and dense. Each vertical lift comes with 43 shelves installed and the capacity to add 20 more, offering flexibility for future expansion.
Due to a high turnaround of parts, the container weighing device ensures safe operation by monitoring tray loads, alerting users to potential overloads, and maximising capacity without risk.
Integrated LED guides and tray optimisation technology ensure quick, accurate retrieval, reducing downtime and improving workshop productivity. No more mispicks, lost parts, or traipsing around a warehouse looking for items. Simultaneous picking capability of the integrated lifts allows operators to retrieve items from one machine while the other prepares the next tray, eliminating bottlenecks.
Perhaps one of the most critical aspects of our vertical lift storage here, is Hänelâs ESB, which ensures that in the very unlikely event of a fault, (such as damage to a light curtain) operations can continue in a number of different ways, depending on the damage caused.
Example: Closed door operation (for added safety) or by returning trays to the same storage location, and removing items only, rather than replenishing or adding new items to shelves. This minimises downtime and ensures critical parts remain accessible while waiting for the local Industore engineer to attend the site.
To enhance security, the Lean-Lifts feature manual, lockable sliding doors, allowing the machines to be secured when not in use, along with access code management, ensuring items can only be retrieved by those with the appropriate permissions. In addition, the light curtain barrier provides maximum safety during operation, ensuring the protection of both operators and stored items. Where items are of a particularly sensitive nature, individual shelves have been programmed to move at a slower speed than the bulk of the shelves, ensuring maximum safety for very fragile items, without slowing down the general operation.
Using CAD plans, Industore was able to clearly demonstrate what success would look like. A detailed layout that included traditional racking for low-value, slow-moving parts, and a mezzanine level for larger, less frequently accessed inventory like body panels was developed, aiding understanding. This holistic approach ensured the entire parts department was optimised for workflow and efficiency, but also ensured that all parties knew what the end-product would work and how it would look.
Project Manager, Steve Anderson-Tyso on the Design and Specification:
“We strategically positioned the Lean-Lifts between the goods-in and goods-out areas, creating a streamlined flow. High-demand, valuable, and/or fragile items are housed within the Lean-Lifts for immediate access, protection and security. Meanwhile, slower-moving, bulkier items like body panels are stored on the mezzanine level, or elsewhere on the racking. This division of storage optimised workflow, allowing parts to move seamlessly through the facility, quickly, but all carefully tracked.”
Ergonomic design principles were also applied throughout the facility. All items in the Lean-Lifts are delivered at waist level to reduce operator fatigue, while traditional racking was itemised to ensure heavier items were never stored at height, enhancing safety and usability.
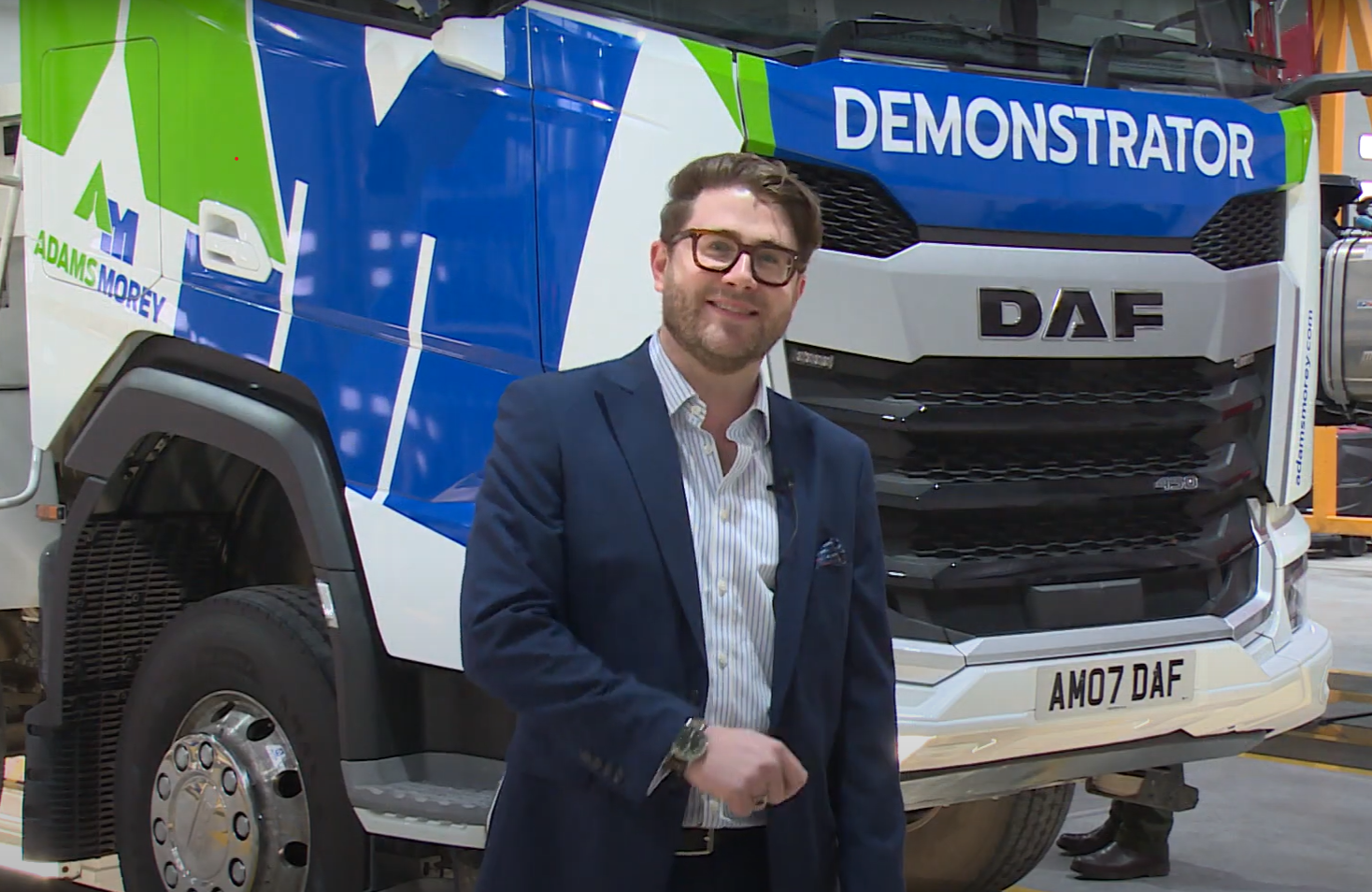
Mick Dean on his experience with Industore:
“Industore absolutely provided a turnkey solution, and in fact, much more than that. The service has been excellent – so good that we invited our project manager, Steve Anderson-Tyso, to our official launch alongside our trusted partners, suppliers, and clients. We have total confidence in Industore and wouldnât hesitate to recommend them.”
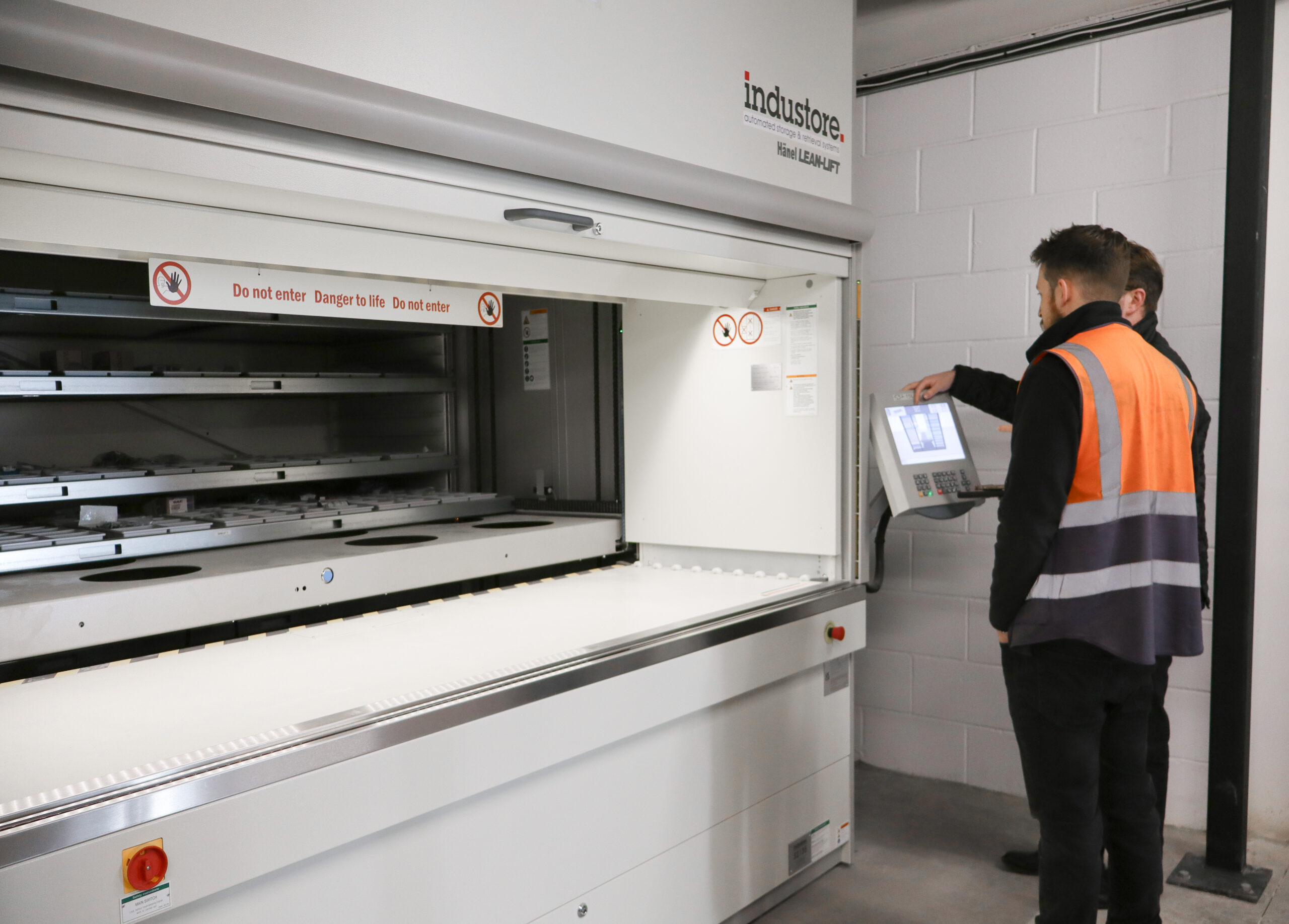