Background
For over a century, Alstom has been a leading light the rail industry and is widely regarded as “the number one operator” in public transportation across the UK – responsible for half of all London’s underground, and a third of daily passenger rail journeys.
Alstom’s Manchester facility, previously had storage systems that were inefficient and constrictive. Traditional racking systems occupied an enormous footprint at the facility, creating an environment which was heavily reliant on manual processes – these were notoriously slower and more error prone than the state-of-the-art solutions offered by Industore.
Due to the enormous headroom available at the facility – the introduction of vertical lift systems was an obvious choice – but ensuring that the machines were specified to the best possible dimensions – to accommodate Alstom’s inventory and day-to-day was a task for Ross Powell, Industore’s Managing Director:
For Alstom, the facility had an abundance of headroom, which was completely underutilised, we immediately recognised the enormous potential to utilise this space with our Lean Lifts, but poor architectural logic is the number one inefficiency that most sites suffer from. While new, cutting edge machinery will always improve operations and productivity, the importance of understanding layout, space optimisation and developing the most efficient design is paramount to maximising success and ROI.”
Project Description:
Following the development of a business case, Alstom conducted a comprehensive market research exercise – comparing a number of vertical, automated storage and retrieval systems (AS/RS) from various suppliers across the UK, and further afield. Finally, Alstom shortlisted two-companies, before inviting them to site to demonstrate their products.
Ross Powell, again:
It was a great pleasure to be asked to demonstrate our products and expertise at Alstom, especially given the market research they had clearly undertaken before approaching us. Ultimately, the Hanel/Industore partnership is a very difficult partnership to top, and once Alstom saw the strength and performance of the Lean Lift, combined with Industore’s track- record, it was going to be a real uphill struggle for any competitor to beat us. I’d back our partnership with Hanel every day of the week.”
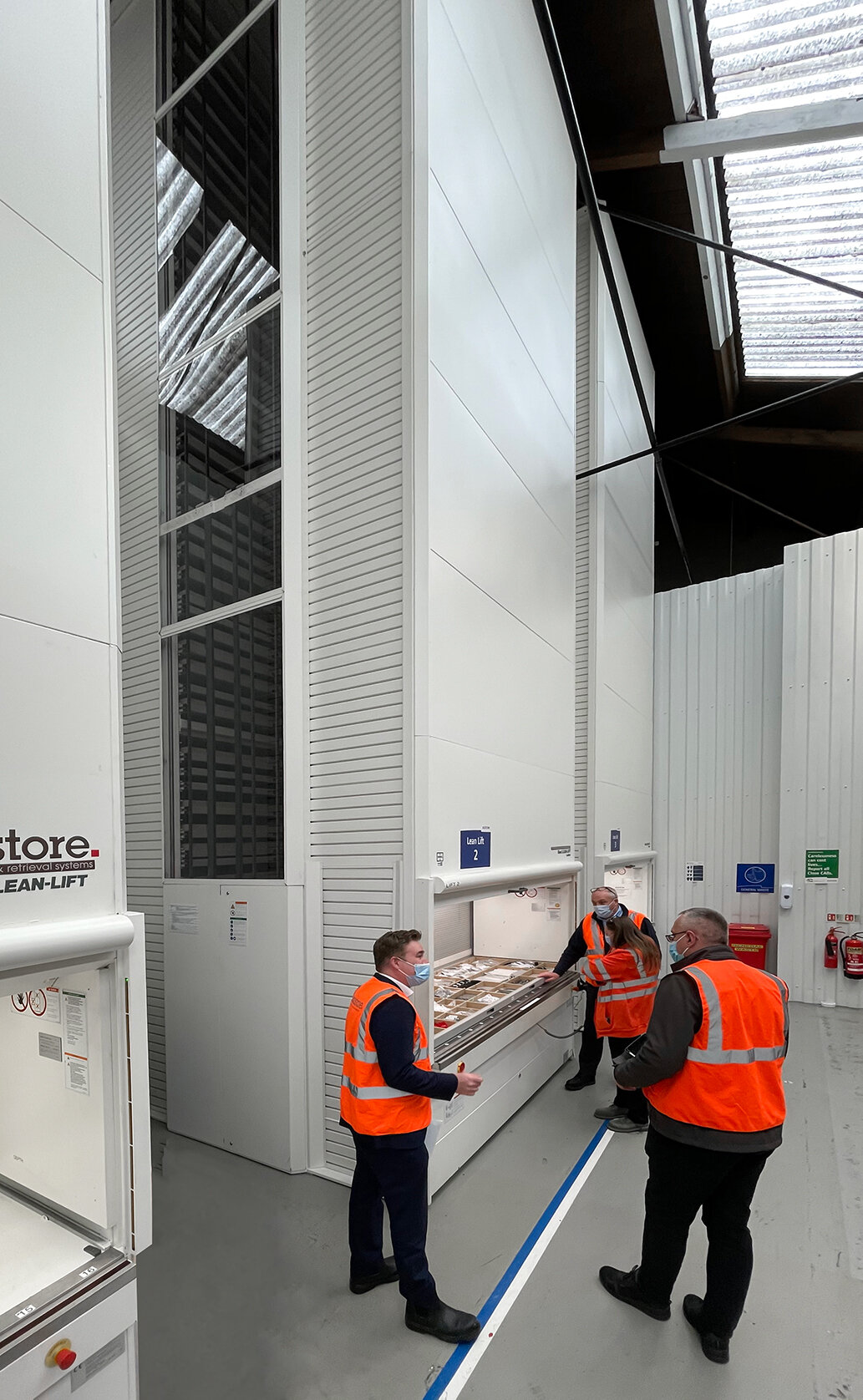
Alstom boast a number of staff who had previously worked in automation and transformation. This empowered the transport giant to make more informed decisions when conducting their market research and shortlisting for demo exercises. Alstom astutely recognised that a number of their 12,000 products were quite large and heavy – something that intuitively, you may not think would suit automated storage and retrieval. While other supplier machines would buckle and bow under the strain, the best in class, durable and robust Lean Lift took the unusual extra load in its stride.
Jason Hughes, from Alstom Transport:
At the demonstration stage of our procurement process, we found that the Industore product was far superior in terms of quality, build and usability than any of the other suppliers we approached. At a very early stage, the leadership and expertise offered by Ross Powell and his team was very encouraging – and since the very first lift was installed, the Hanel/Industore partnership has been one that has continued to deliver.”
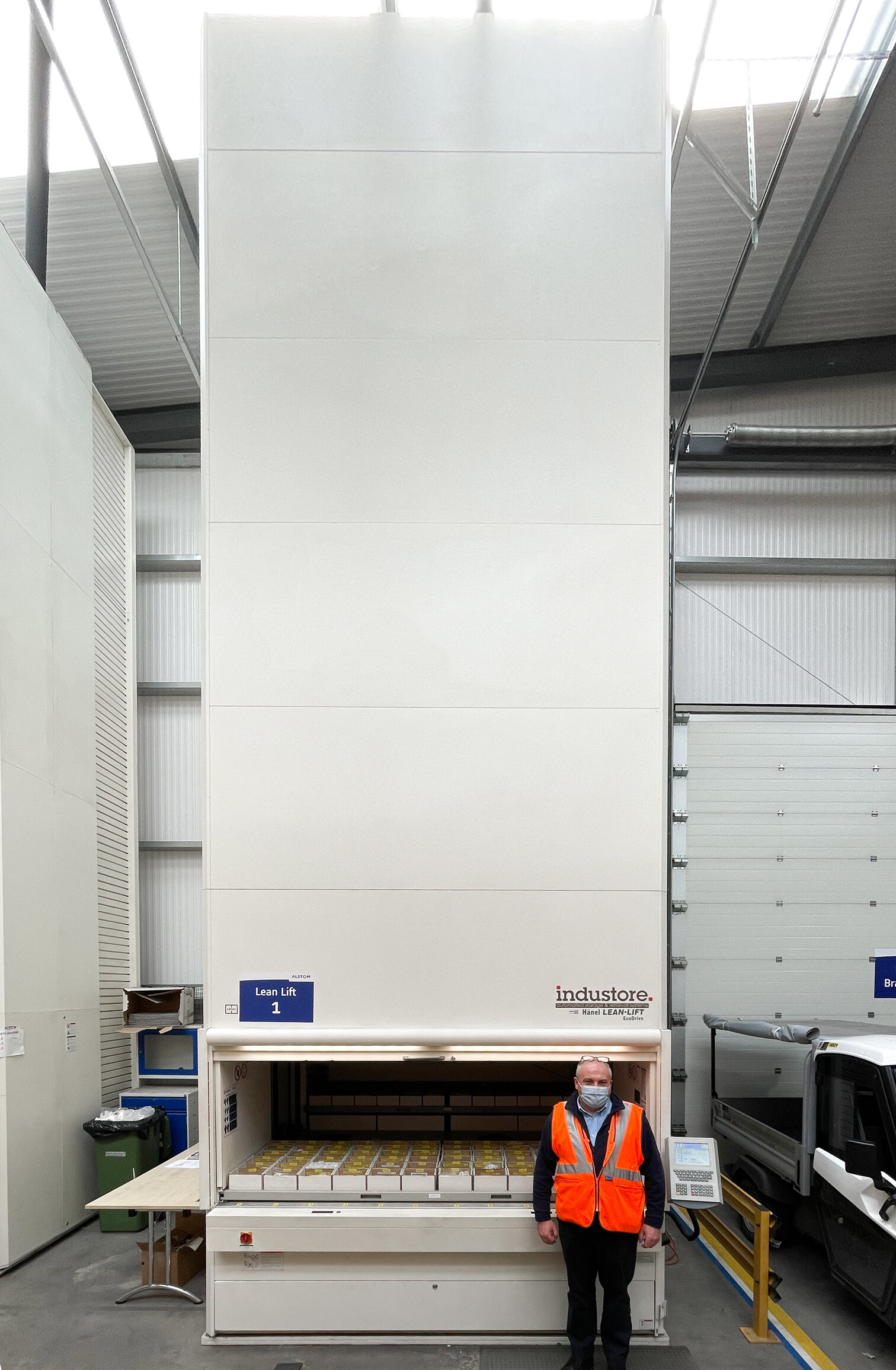
Post Installation:
Alstom is now making the most of their enormous ceiling height – with a number of Lean Lifts situated at the facility’s tallest point. This allows the machines to take up a tiny footprint, while increasing stock capacity, as well as speed up storage and retrieval, stock transparency and guarantee an entirely accurate audit trail 24/7/365. Furthermore, where in the past, Alstom’s stock was reviewed and replenished up to 15 times a day, the transparency provided by the Lean Lift’s Microprocessor Control System has reduced this to a single drop off per day – saving an enormous amount of downtime, energy and money in the process. In place of boots on the ground running up and down mezzanines to replenish stock, today, items are simply loaded and logged into the Lean Lifts via the access draws – safer, faster, more accurate than ever and much, much more efficient.
Camera integration has created a visual diary that has sped up the picking process enormously. This Manchester facility is home to the multiple maintenance teams, who work day in day out on train repairs, builds and more. Quick access to the correct part is absolutely vital to their operation and the day-to-day transportation of half the country. The installation of automated storage has reduced a three-person stock team to a single employee – retrieving and booking out critical parts in seconds, and the performance is better than ever. Furthermore, the excess staff on the stock team have been repurposed to elsewhere in the organisation, where they are completing much more fitting, and beneficial roles.
Results
Alstom is widely regarded as the most revolutionary train depot in the UK – possibly in Europe. Driven by an ambition and enthusiasm to really break the mould and retain the legacy they’ve developed across the rail industry, Alstom’s partnership with Industore has grown from strength to strength. As the future of logistics and rail develops in the post- Covid and post Brexit world, the need for uninterrupted, reliable and more competitive operations is at clear for all to see. With a partnership built on trust and joint ambition, Industore and Alstom continue to work together at pace – developing innovative and creative solutions. We look forward with great excitement to the next install.
Seventeen Hänel Lean-Lift across the UK
Reasons for investment: