Essilor first opened its doors nearly 175-years ago in Paris. Today, the now global business is widely regarded as the premiere manufacturer of optical lenses anywhere in the world and is the world’s largest manufacturer of ophthalmic lenses. With an expanding international presence and an ever-increasing call on demand, a Republic of Ireland distribution facility was erected.
Introduction to Essilor
Essilor’s distribution facility comprised office space, research and production laboratories as well as, a large warehouse. When Industore first visited the centre in County Clare, the antiquated storage system in use demanded an enormous chunk of the total facility footprint. As demand increased, Essilor turned to Industore to rationalise their warehouse footprint – while maximizing storage capacity. Large amounts of very high stacked racking meant Essilor was heavily reliant on manual picking and storing processes, which resulted in slow pick times, and too often, breakages of high value items as staff stretched to reach item stored above chest-height. At the time Industore was asked to develop a solution to solve Essilor’s expanding requirements and manual handling errors, the company employed a number of staff whose sole purpose was in stock checking and documenting product codes, all of which was completed by hand, on paper. Expensive, time consuming and error-prone.
Trevor Elliot, Ireland Sales Director:
During my initial visit in the early 2000s, it was evident that Essilor’s storage area was not working for them. The traditional racking system took up an enormous amount of space – including wasted high-level space which was storing nothing but fresh air. An entire team of pickers would spend hours upon hours in the warehouse checking, counting and documenting stock details on paper, which is always extremely time-consuming, miserable work, often erroneous.”
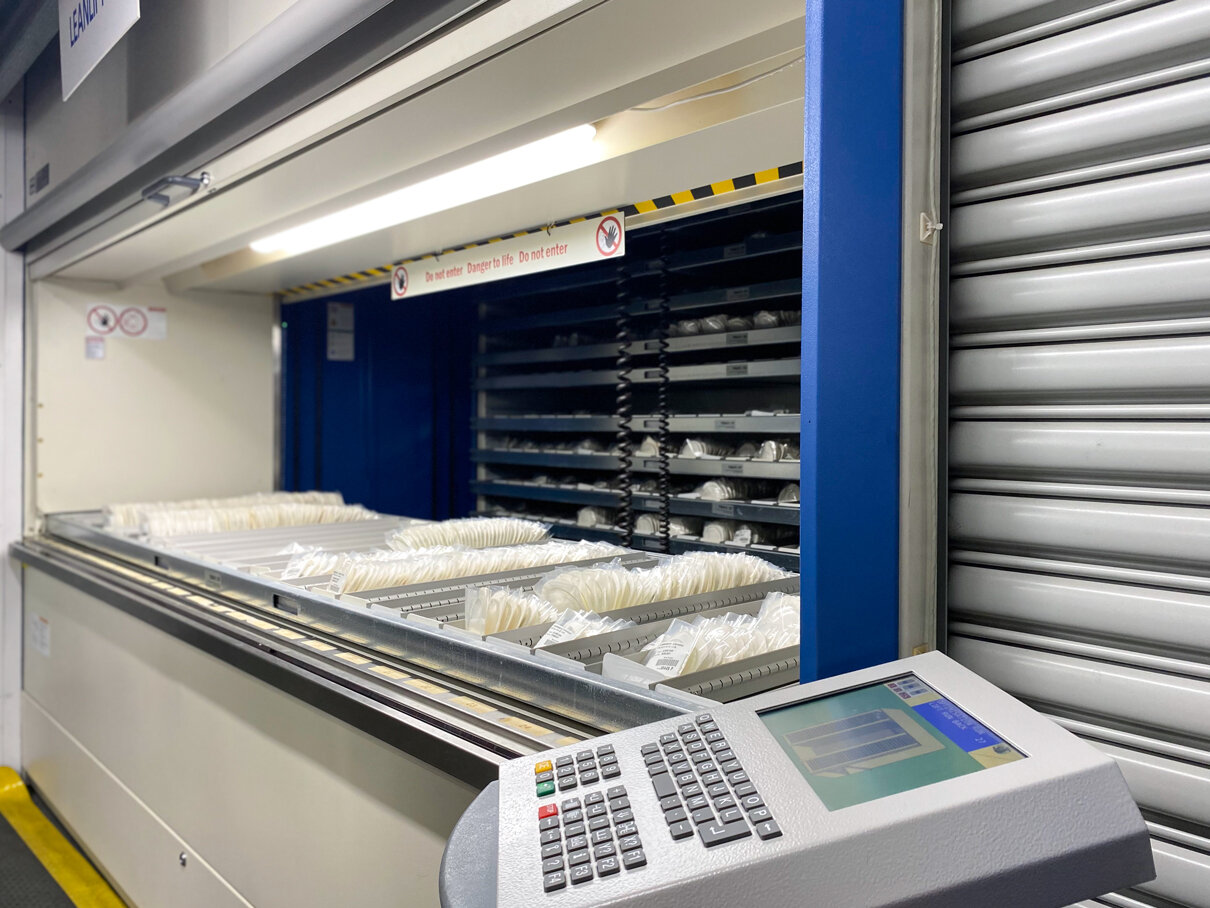
Project description:
As well as recognising some simple, quickly implemented improvements which would be achieved by introducing automated storage and retrieval systems (AS/RS), Ireland Sales Director, Trevor Elliott applied his hard-won architectural logic to identify space-improvements, which would add to the enhanced efficiency Essilor sought. Identifying the best place to install the lifts, an area near the rear of the building – where deliveries of inventory were unloaded frequently, Trevor measured the full head-height available, and commissioned a 6m high Hänel Lean-Lift with 64 trays. This allowed to storage of 800 lens moulds per tray, giving a total of over 51,000 lens moulds in a footprint of just 10.13m2. To put this into perspective, the equivalent storage space required for traditional shelving would have been close to 120m2.
Following the installation, Essilor immediately began to feel the enormous benefit of Industore’s implementation. As a result, another two machines of the same specification were installed inside a year. Now, all three lifts store the fragile and highly valuable optical lenses securely on 192 trays – and access is restricted to authorised personnel, via secure card-reader on the reverse of the controller unit, enhancing security. For greater stock transparency, Essilor uses the MPN12 controller to track inventory quantity and monitor/track storage locations at the press of a button – significantly reducing manual workload and saving valuable time, while benefiting from the “knowing who took what, when” system, provided by the technology.
Hanel Soft:
The integration of HänelSoft transformed Essilor’s approach to inventory storage. Data recorded by the Lean-Lifts extended further than the MPN12 controller. The software enables employees to access inventory data through a secure, online network – which essentially means it could be accessed from anywhere in the world. That means, if a global pandemic were to strike, for example, Essilor could continue to operate entirely successfully with only a skeleton crew physically operating the lifts. Administrators (given appropriate access permissions) from anywhere with an internet connection could check on progress, monitor stock levels, add/remove jobs and more with complete ease. Through clever tray mapping, Essilor can now configure their inventory to guarantee the most efficient use of storage. The intelligent system will calculate an access and storage percentage after returning the tray in the best space-saving position. This will allow the software to identify which trays are most frequently used, and store those trays nearer the front of the Lean-Lift, enabling the fastest possible retrieval. The solution holistically has resulted in an enormous efficiency improvement for Essilor – which has been realised by all who work there.
The Results
Since Industore’s full implementation, Essilor have achieved their primary goals of increasing capacity and reducing their warehousing footprint. Warehouse pickers’ time is much more efficient and inventory control is at its best ever. Simultaneously, breakages and losses are at their lowest since operations began. This ambitious and forwardthinking company have succeeded enormously in creating a much less claustrophobic atmosphere, as all very high racking has been removed from the warehouse, creating a happier working day for their employees. Previously, stock checks required the full attention of an entire team. Now, a single picker is able to undertake and complete this process – and even more impressively, complete the task in half the former time. Perhaps most significantly, Essilor’s lead planning time has been decreased by 24-hours – gaining the company a day a week of production and business time. Industore’s relationship with Essilor continues in the form of an annual aftercare plan, and the relationship now extends beyond Ireland, into the UK.