Optimising Warehouse Efficiency with Industore at Sonardyne International
Sonardyne International is a global provider of underwater acoustic, inertial, optical, and sonar technology. The organisation relies on an efficient warehouse to support its operations in the offshore energy, maritime security, and defence industries (etc.). As demand began to outstrip capacity within the warehouse, Sonardyne partnered with Industore Limited; to make the warehouse’s square metres work harder – and introduce a new warehouse management system (WMS) to improve inventory control.
Prior to implementing the Industore Lean-Lifts and HänelSoft software, Sonardyne encountered several challenges in its warehouse management. The need for accurate and efficient picking processes was critical due to the high value and specific requirements of the parts used in Sonardyne’s products. With over 20,000-part-numbers to manage and a fast-paced working environment, Sonardyne required a solution that would ensure accurate picking, traceability, and quick access, while maximising space utilisation within its facility. Moreover, as the warehouse was being consolidated into a smaller working area (allowing expansion of other areas of the business), the company had no choice but to investigate alternative, improved storage solutions.
Following a thorough go-to-market exercise, Sonardyne named Industore as their preferred solution provider, with a view to optimising warehouse efficiency. Regional Project Manager, Steve Anderson Tyso explains:
“The task was a challenging one. Sonardyne required enhanced warehouse capacity in a shrinking space. Following comprehensive data analysis with the client – getting a clear idea of quantities, sizes, movement patterns and more, I was able to propose an ideal solution, and allow room for future expansion. The implementation process involved careful planning and coordination to ensure minimal disruption to Sonardyne’s on-going operations, which included a phased installation schedule to ensure production continuity and minimal disruption.”
The Lean-Lifts were integrated with HänelSoft, Industore’s proprietary software, to act as the warehouse management system (WMS) and stock-keeping. The utilisation of vertical space with the Lean-Lifts resulted in a substantial increase in floor space, allowing for efficient allocation of resources within the facility.
Optimising Warehouse Efficiency – The Results:
Today, each tray inside our Lean-Lift provides over 2.5m². With 60 in each lift (and room for expansion), there is currently over 300m² of parts in storage, in a footprint of just 17m². Were these parts stored in the (now smaller) warehouse on racking, there would no longer be sufficient storage space, as the lifts have improved the storage effectiveness by over 75%. This calculation has been based on standard 2,700mm x 600mm racking with four levels, offering less than 6.5m² of storage at roughly 60% effectiveness. In a real-world working setting, it is more likely that this figure would be significantly lower, requiring upwards of 50 bays, which would in turn require over 150m² of footprint – and still fail to generate any of the additional benefits of automated storage and retrieval systems (AS/RS), such as…
- Increased accuracy in inventory management
- Faster picking and restocking processes
- Reduction in workplace accidents
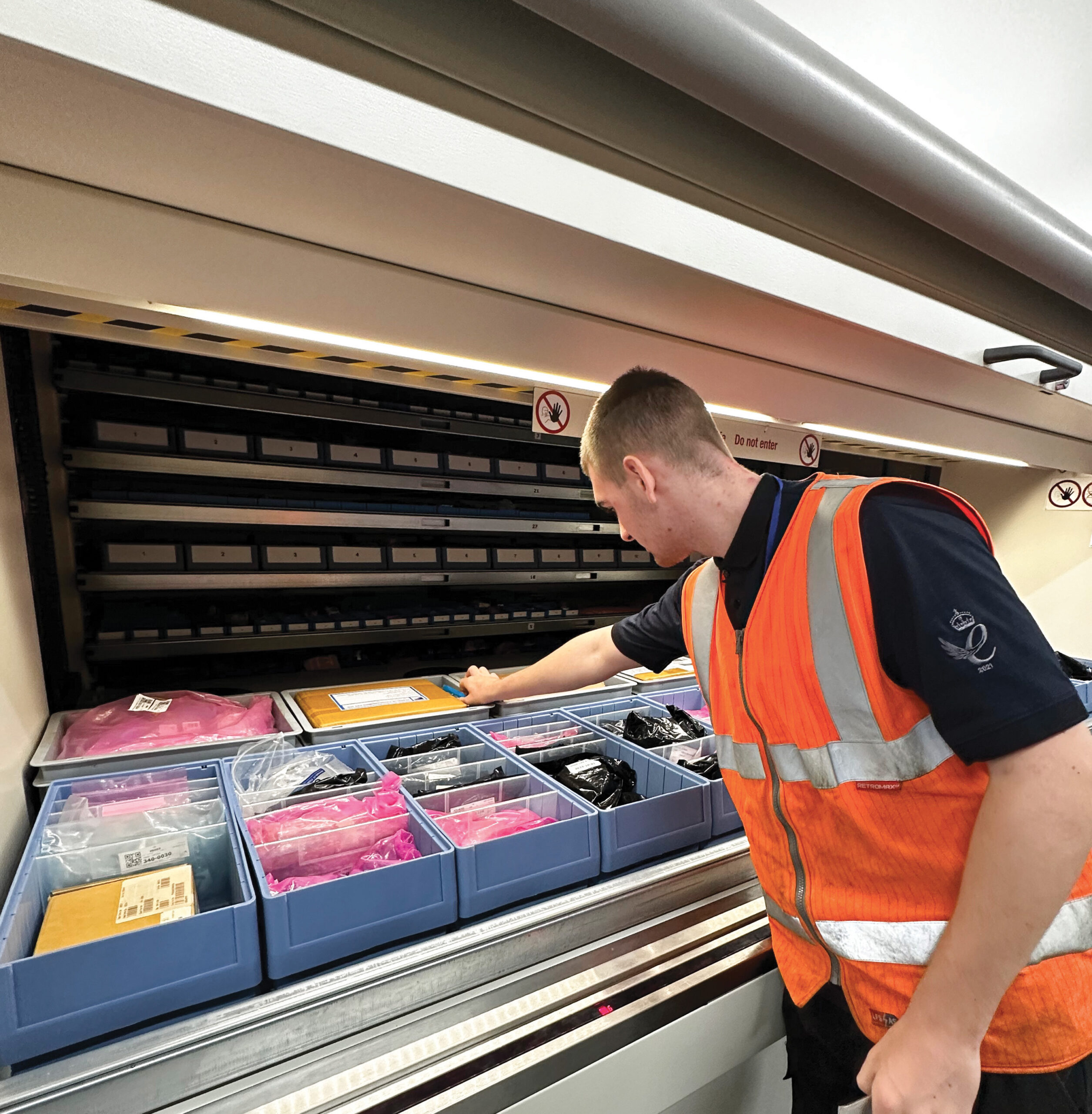
Sonardyne’s stock management (ensuring the right parts are always in stock, and that there is never an overorder) was already exceptionally high, reaching a peak of 99.8% in 2023. By implementing the Lean-Lifts and the HänelSoft solution, Sonardyne has increased this to the illustrious 100% inventory control. Since the implementation of the lifts (and HänelSoft), there has yet to be a misorder or misplaced item. Moreover, Sonardyne has reduced picking errors from 0.2% to 0.06%. An improvement of 70% – as Warehouse Manager, Mark Dixon explains:
“We’ve always taken enormous pride in our stock management and our pick accuracy at Sonardyne. Last year, we averaged one mispick for every one thousand orders – today, thanks to Industore, that’s down to one mispick every 60 thousand orders. Really, we’re at a point now where we just say we’re at 100% picking accuracy, and that is absolutely down to the Lean-Lifts and the HänelSoft system specified, installed, and maintained by Industore.”
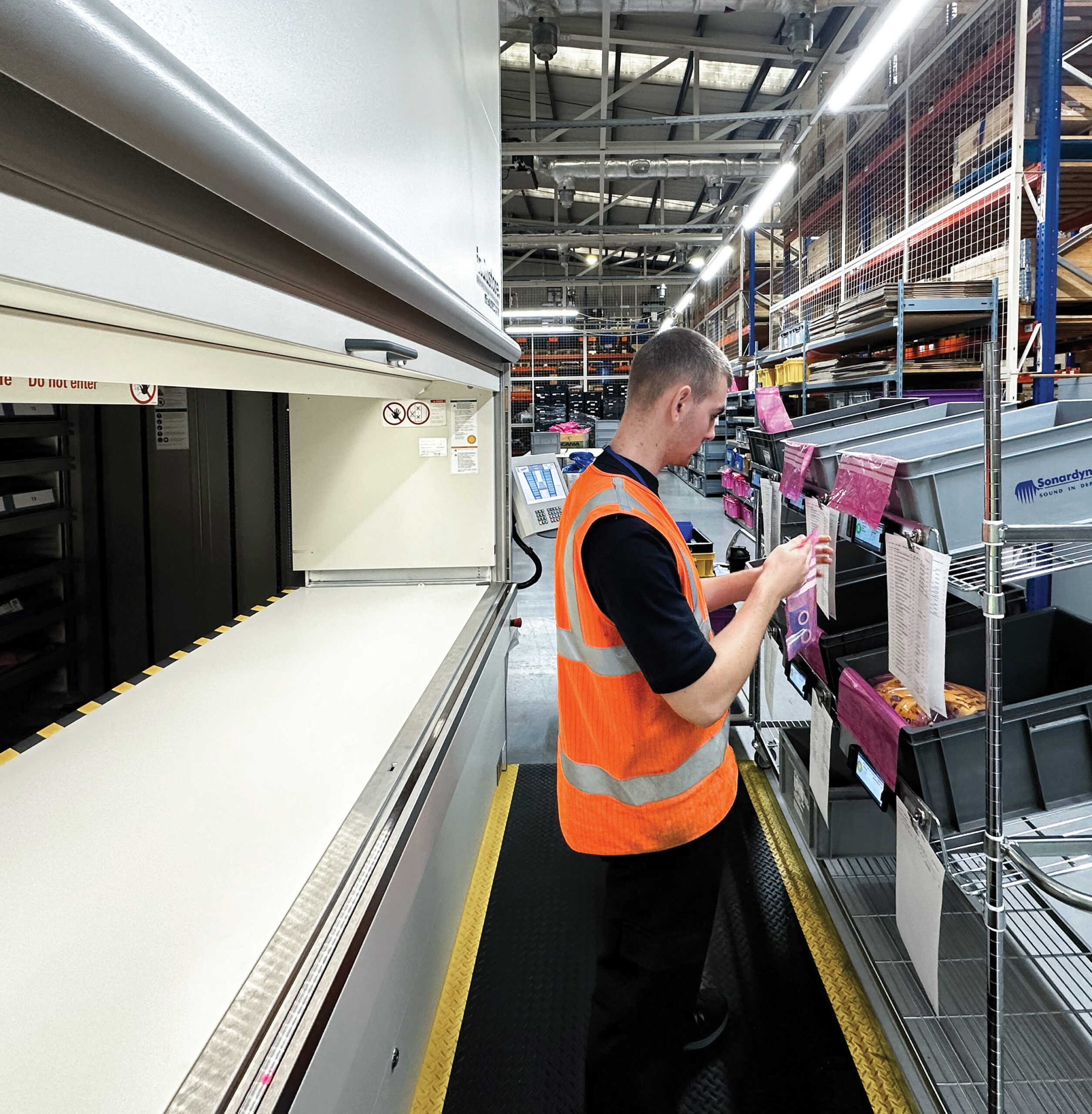
Increasing warehouse pick rates:
Implementation of HänelSoft has facilitated enhanced traceability and batch picking, enabling Sonardyne to run 12-jobs simultaneously, significantly increasing throughput and productivity as well as reducing operational time and picking resource. The software’s pick and put-to-light system, coupled with visual aids such as pictures and notes within the software, has contributed to pick and restocking accuracy and made the warehouse staff role much easier, and yet more dynamic and enjoyable. The flexibility of the HänelSoft software has enabled Sonardyne to customise FIFO (first in, first out) processes in a way that suits them, giving some parts strict FIFO protocols, some with no FIFO preferences, and some with broader considerations, such as ‘prioritise efficiency first, then FIFO protocols,’ for example.
Safety is of utmost importance for Sonardyne. Now with no need for ladders, thanks to the ergonomic, goods to person (formally G2M) design, the risk of workplace accidents has all but disappeared. All items in the Lean-Lifts are now delivered at an ergonomic height, with no need to stretch or bend. An added benefit of this is that inventory loss and breakages have also decreased. The safe and intuitive nature of the Lean-Lifts (and the software integration), combined with the speed improvements in throughput, has also allowed for easy onboarding of new staff members, or even general staff within Sonardyne, at times of heightened demand on the warehouse – further optimising warehouse efficiency, and throughput, when the occasion calls for it.
The success of the Lean-Lifts and HänelSoft implementation at Sonardyne has garnered strong endorsement from the company’s senior management and stakeholders – with the plexiglass side making a dramatic vista for all visitors, watching the extractor store and retrieve products in the blink of an eye. Sonardyne is currently in conversations with Industore about additional units, not only on this site but elsewhere, indicating the company’s confidence in the effectiveness of the solution. This has been helped by Sonardyne’s positive experience with Industore staff. Mark Dixon, again:
“The solution itself, the hardware and software, is just brilliant, but I have to mention our experience with Steve Anderson-Tyso – our project manager, and Stephen Froude – one of Industore’s technical, HänelSoft advisors. Both these guys are clearly at the top of their game. Steve worked with us steadfastly to ensure we had the perfect solution. There was really nothing he didn’t think of, and he did a lot of homework – he knew the company inside out before proposing a the lifts we have today. The same can be said of Stephen Froude. He was able to speak to just about anyone in the business, regardless of their level of software experience or expertise. In as much or as little detail as we wanted, he could answer every question with confidence. It’s all exactly as we expected – perhaps a little better!”
By implementing Industore’s Lean-Lifts and HänelSoft systems, Sonardyne have achieved remarkable improvements in stock accuracy, picking efficiency, space utilisation, as well as overall warehouse safety – this, in spite of the organisation’s already exceptionally high levels of success. The collaboration has entirely addressed Sonardyne’s short-term challenges, but more than that, has future-proofed the organisation – perhaps even assisted in reassessing growth plans, but certainly optimising warehouse efficiency.