Until recently, like many other NHS trusts, University Hospital Birmingham rented a number of storage facilities to archive patient files with support from approved external storage suppliers. As well as costing the taxpayer storage fees, this arcane process was error-prone, difficult to manage and slow-moving.
Thanks to the innovative vision of Head of Warehousing & Logistics, Dave Lightening, this pioneering NHS Trust has now modernised, rationalised and centralised their storage with Industore – implementing six, ten-meter automated storage and retrieval units for fast-moving files. Furthermore, a combination of market-leading, modern software technology and well-organised VNA (very narrow aisle) racking has facilitated a much improved management of older, slower moving files and truly optimised use of space for better speed and precision.
On top of improved security, a reduction of the overall warehousing footprint and a future-proofed service, this venture has empowered the University Hospital to save money on renting through third parties, and has allowed a much faster, smoother transfer of patient files from storage to doctor hands – potentially saving lives.
Along with the new archive storage solution, Industore also worked with logistics staff of the Trust to enhance their operation, by introducing further, specialised racking solutions – empowering the Trust to face, with confidence, “The Integrated Care System” – which came into force in April 2022. The new facility has given Dave and the team over 3,000 pallet storage locations on top of the archive storage, which has strengthened – enormously – the Trust’s ability to serve all patients and care systems to the highest possible standard.
Key Benefits
Before the project started, we set an ambitious target of transferring 11,000 files a day. Thanks to Industore, we’re now hitting 16,000 a day. That’s been achieved because of the technology and the support from the Industore team. The clear stage-gates and timeline, the honest pricing and support is why I am an Industore advocate – and wouldn’t hesitate to recommend them.”
Dave Lightening, Director of Warehousing & Logistics UHB University Hospitals Acute NHS Trusts.
Software integration:
University Hospitals Birmingham NHS Foundation Trust (UHB) is widely regarded as one of the highest performing acute trusts in Europe – with a proven international reputation for quality of care, information technology and more. The Trust uses the Oceano patient administration system (PAS) to document their electronic patient records (EPR). Industore’s broad integration abilities allow us to work with just about any existing software application, as well as offer our own highly configurable, scalable integrated management system (IMS).
For this Midlands application, anyone with appropriate access to the Oceano system can now request patient files as they always have, which will trigger Industore’s application. From GPs to ward nurses and more, no additional learning has been required, as the Industore system sits below the Oceano system all staff are familiar with. Once a patient record has been called, Industore’s clever integration technology sets to work, instructing operators of both the warehouse Lean-Lifts and Man Up trucks through very narrow aisle racking (VNA).
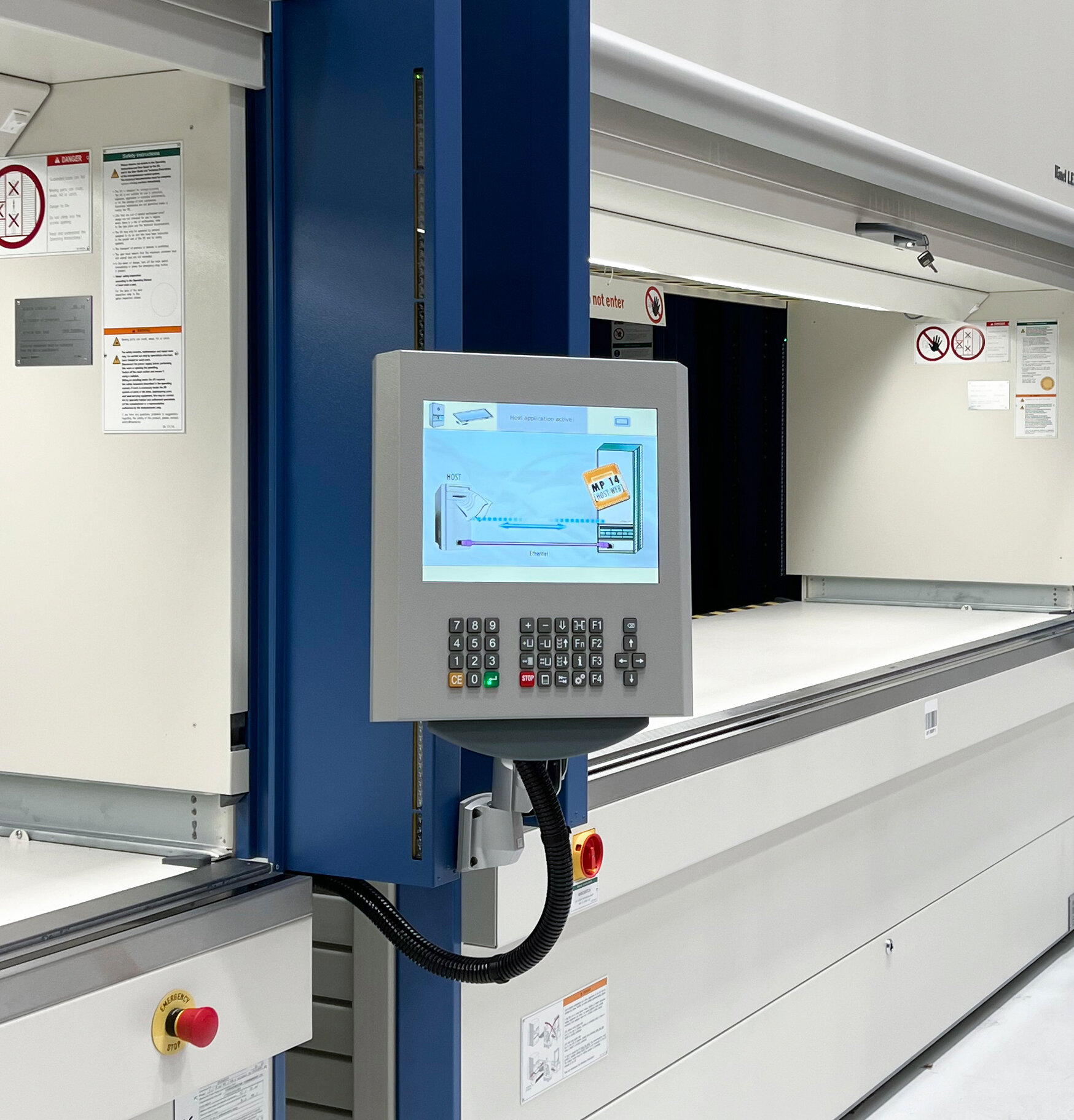
Lean-Lift retrievals:
The Lean-Lift retrieval process is largely an automatic one. For the benefit of security and traceability, an operator must sign into the Lean-Lift, in order to gain access to any files – in this case, with a username and password, though other methods (such as RFID cards) are available. The operator is then instructed, either to ‘store’ or ‘retrieve’ – and the machine acts accordingly.
The first shelf is brought to the picker and presented at a comfortable, ergonomic height for both health and safety, and optimum performance. To ensure maximum efficiency, pick-to-light technology indicates the correct location of the required file, and the operator collects that file, scanning the associated barcode attached; thereby reducing the margin of erroneous retrieval to zero. From here, the Lean-Lift prompts the operator to indicate whether the retrieval is for ‘housekeeping’ (being moved elsewhere in the warehouse) or ‘dispatch’ (being moved to a designated location such as a hospital or GP surgery). The Lean-Lift then moves to the next file location – either on the same shelf, or another. If the same shelf is required, the pick-to-light indicates where the next file is stored, if not, the operator is prompted to enter the new ‘remaining capacity’ of the presented shelf; for future storage/retrieval space. Once complete, the presented shelf is stored, and the next shelf is presented to the same, ergonomic location – for the process to repeat.
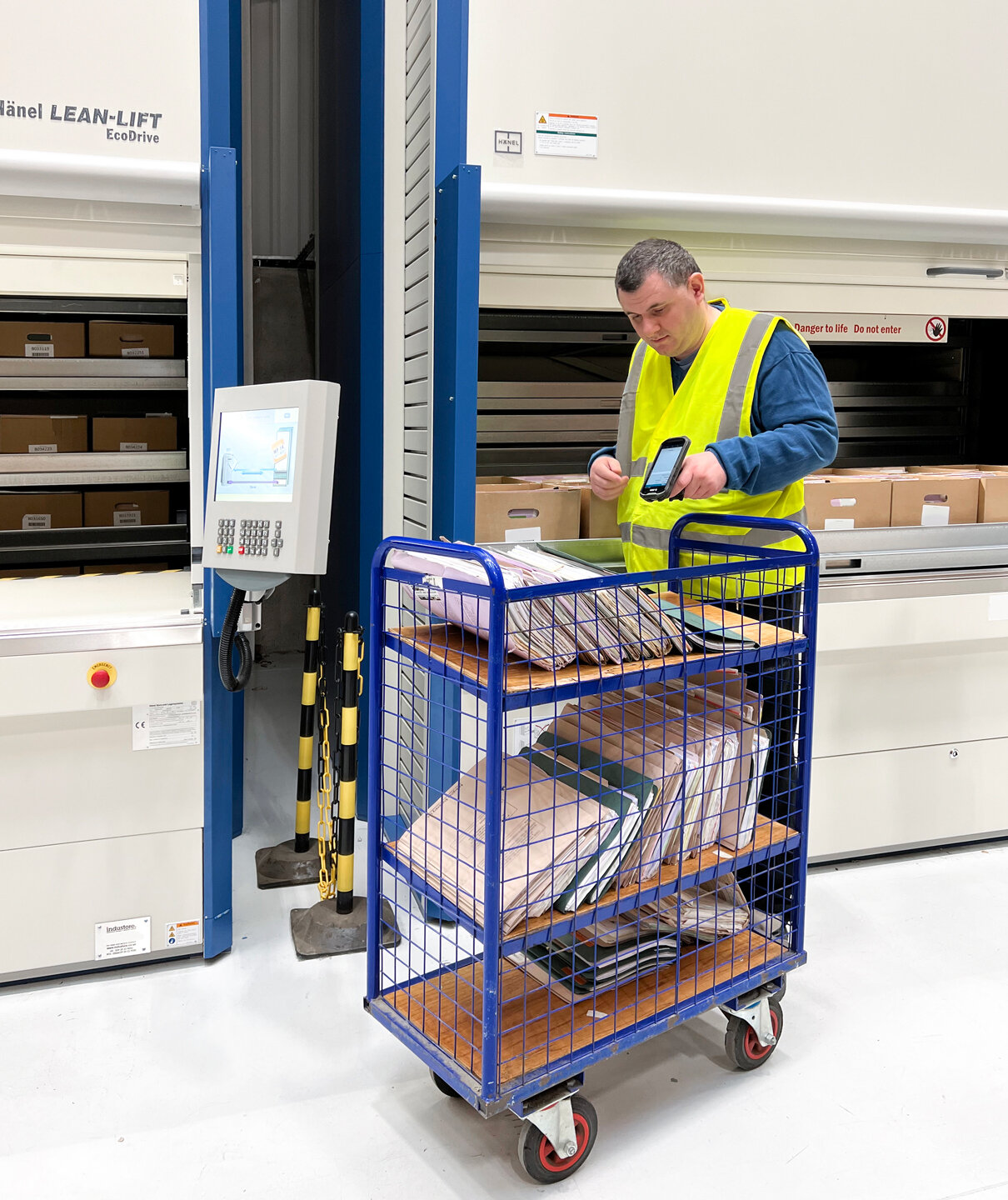
Lean-Lift storage:
In storage mode, by default, the Lean-Lift will always select the shelf with the largest available capacity. At this point, the operator is prompted to scan the file barcode, then return it, scan the related box to confirm, and finally, associate the location. The system will then ask the operator to estimate the new remaining space available in that given box for future storage. The process then continues until all the files are stored.
Racking retrieval:
If a patient file hasn’t been retrieved for some time (a ‘slow-moving file’), it will likely be located on the VNA racking, which works alongside the Lean-Lift technology. Once a patient record has been requested, the software will plot the fastest, least disruptive course around the racking, and the Man Up Truck will automatically be taken along the pre-plotted route, via wire guidance. Wire guidance all but eliminates the risk of accidental human error, optimises the lift speed and restricts any deviation from the centre of the track – significantly improving site safety. Depending on the vertical location of the file, the truck will automatically begin to ascend (or descend) to the appropriate height for perfect ergonomic retrieval of the file(s). Furthermore, Hänel’s vario pick-to-light indication system indicates the exact archive box where the required patient file is stored, reducing wasted time to virtually zero. From here, a barcode (located on every patient record) is scanned by the worker (with an intuitive, handheld controller), giving final confirmation that the appropriate file has been selected- removing all margin for error – potentially saving lives.
Patient files can vary in length from a single sheet of paper to an elaborate, lengthy set of documents, measuring inches in thickness. To ensure that no boxes are filled beyond reasonable capacity (and crucially to ensure no space or time attempting to return the file is wasted), the driver will now estimate the capacity remaining in the document storage box.
This allows the technology to recognise the remaining space for additional capacity for future use. From there, the box is replaced to the appropriate racking space, and the Man Up Truck continues to the next pick location. Efficient, effective and safe. Once a patient file is finished with, it can be returned to the warehouse. On arrival, the file will be placed directly into the Lean-Lift – regardless of where it was collected from. The Lean-Lift allows for much faster storage and retrieval than the VNA racking, and statistically, a file is more likely to be retrieved more than once in three months than not. Once a record has been stored in the Lean-Lift for an extended period of time; without being recalled (a duration defined by administrators), it is replaced to the slower moving section of the warehouse – the VNA racking.
Racking storage:
At a scheduled time, every day, the system automatically generates requests to withdraw items from the Lean-Lift for housekeeping – which is essentially notifying the operator that a file has been in the Lean-Lift for the appropriate amount of time, and can now be placed on the VNA racking instead.